Workplace injuries are a persistent issue in the manufacturing industry, with a noticeable increase in incidents towards the end of the first quarter of each year. A report by the Workplace Safety and Health Council (WSHC) highlighted this trend, raising concerns about how businesses can mitigate these risks.
Among the various causes of workplace injuries, poor ergonomics is a contributor, particularly in the form of musculoskeletal disorders (MSDs) caused by repetitive movements, awkward postures, and improper workstation designs. By integrating ergonomics into machinery design and daily operations, companies can create a safer and more productive environment for workers.
Let’s explore why injuries increase, who is most affected, what ergonomic solutions exist, and how businesses can implement them for long-term safety and efficiency.
Why Are Workplace Injuries Increasing in Manufacturing?
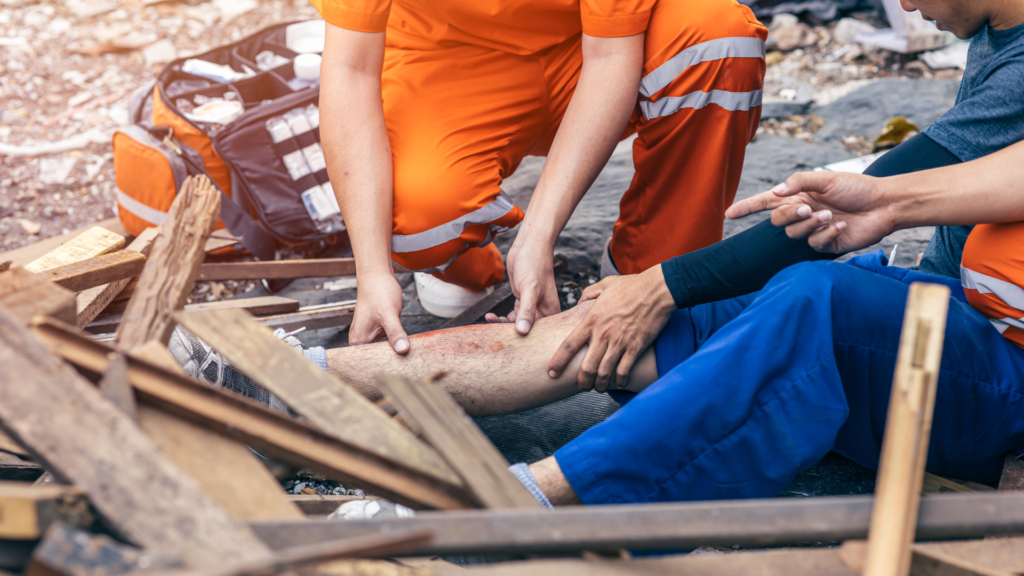
Here are several factors that may have contributed to workplace injuries:
- Increased production demands
Many companies ramp up operations after the holiday period, leading to longer work hours and increased physical strain. - Workforce fatigue
Employees returning from leave may take time to readjust to physically demanding tasks, increasing the likelihood of accidents. - Lack of adequate safety training
New hires or temporary workers may not be fully trained in proper workplace ergonomics and safety protocols. - Complacency towards safety measures
Routine tasks might lead to unsafe shortcuts, especially if machine designs do not consider ease of access for maintenance and operation.
Who Is Most Affected by Workplace Injuries?
Workers in the manufacturing sector who are involved in manual material handling, machine operation, and assembly line work are at the highest risk.
- Machine Operators
Handling heavy equipment, repetitive motions, and awkward postures contribute to injuries. - Assembly Line Workers
Standing for long hours, bending, and reaching lead to back, neck, and limb strain. - Maintenance Staff
Poorly designed safety guards or hard-to-access machinery can result in unsafe workarounds. - Warehouse & Logistics Workers
Lifting, stacking, and moving inventory without proper ergonomic tools leads to MSDs.
By addressing ergonomic risks in these roles, companies can significantly reduce workplace injuries and enhance productivity.
What Are the Common Injuries Linked to Poor Ergonomics?
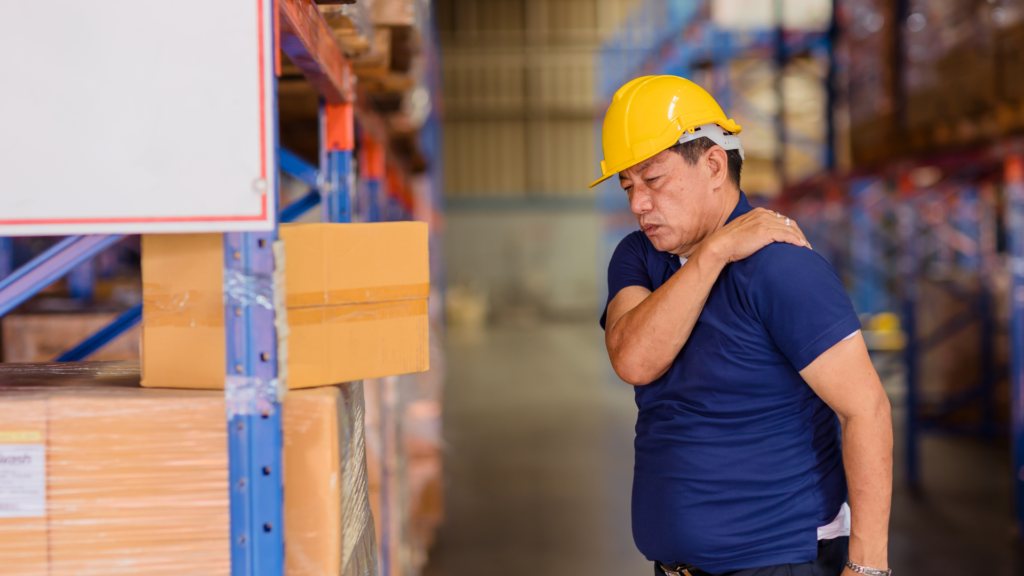
When ergonomics are overlooked, employees are prone to various work-related musculoskeletal disorders (WMSDs), including:
- Shoulder & Neck Pain
Often due to reaching overhead or using non-adjustable workstations. - Hand & Wrist Injuries
Repetitive motion tasks without proper tool design lead to carpal tunnel syndrome and tendonitis. - Lower Back Strain
Caused by improper lifting techniques or prolonged standing. - Knee & Foot Problems
Standing for extended periods without adequate foot support results in joint pain.
To reduce these injuries, businesses must redesign workstations and processes with ergonomic principles in mind.
Where Can Ergonomic Improvements Be Made?
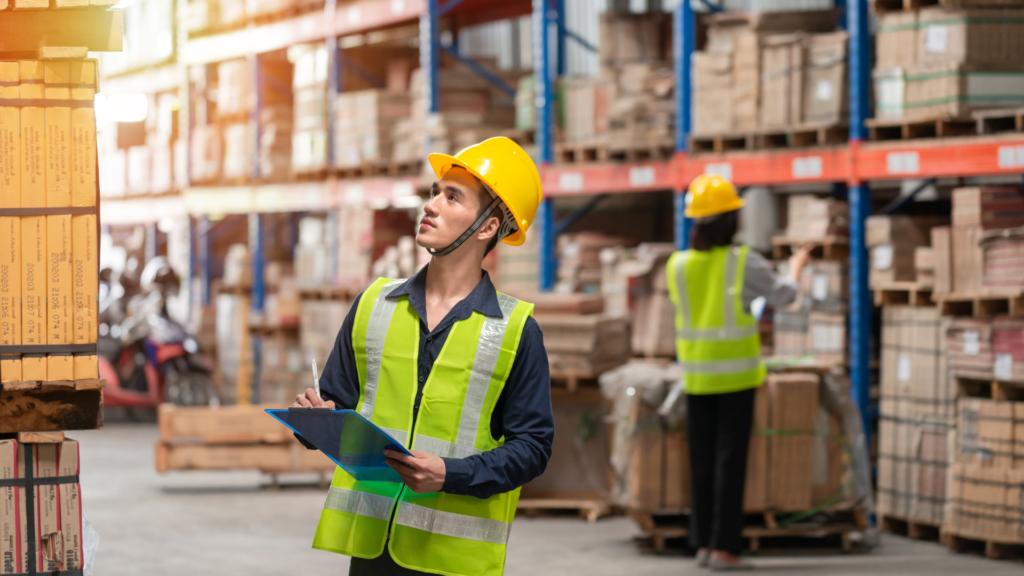
Ergonomic enhancements should be applied wherever repetitive motions, prolonged standing, or heavy lifting occur. Key areas include:
- Machine Design & Layout
Ensuring control panels are positioned at an optimal height to prevent excessive bending or reaching. - Workstation Adjustability
Implementing height-adjustable tables and ergonomic seating to accommodate different body types. - Material Handling Processes
Introducing conveyor belts, lift-assist devices, and wheeled carts to minimise manual lifting strain. - Training & Awareness
Educating workers on proper posture, lifting techniques, and the importance of taking breaks.
By optimising these areas, companies can significantly reduce strain-related injuries and improve worker comfort.
When Should Companies Implement Ergonomic Strategies?
The best time to start is now! But for effective long-term impact, companies should:
- Conduct regular ergonomic risk assessments
- Identify high-risk tasks and workstations every quarter.
- Introduce ergonomic interventions during new equipment purchases
- Ensure machines are designed with safety and usability in mind.
- Ensure machines are designed with safety and usability in mind.
- Provide ongoing training
- Incorporate ergonomic awareness into employee onboarding and annual refresher courses.
- Incorporate ergonomic awareness into employee onboarding and annual refresher courses.
- Monitor injury trends
- Use data from past incidents to adjust policies and prevent recurring injuries.
- Use data from past incidents to adjust policies and prevent recurring injuries.
Consistently integrating ergonomics into workplace policies will foster a culture of safety and injury prevention.
Conclusion: Prioritising Ergonomics for a Safer Workplace
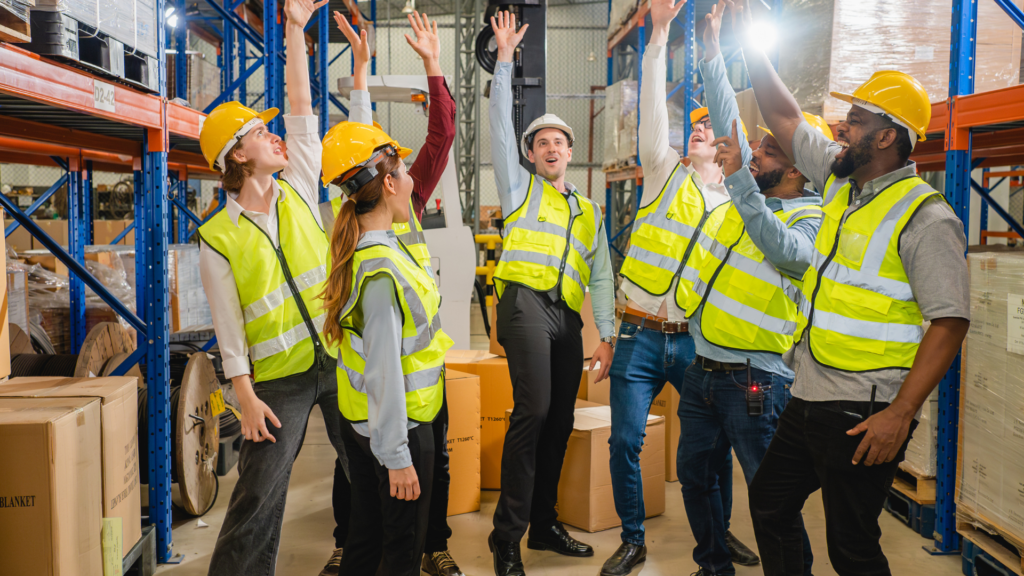
Workplace injuries in the manufacturing industry continue to rise, especially towards the end of Q1 each year. By focusing on ergonomics, businesses can reduce musculoskeletal disorders, improve worker productivity, and enhance overall safety.
Instead of merely installing machine guards or safety barriers, businesses should consider how employees interact with their environment. Ergonomic machine design, adjustable workstations, and proper training can create a healthier, injury-free workplace.
A safer workplace starts with better ergonomics. Are you ready to improve your workplace safety? Let’s make it happen today!
📌 Need expert guidance? Contact us to learn more about ergonomic risk assessments and workplace safety solutions!